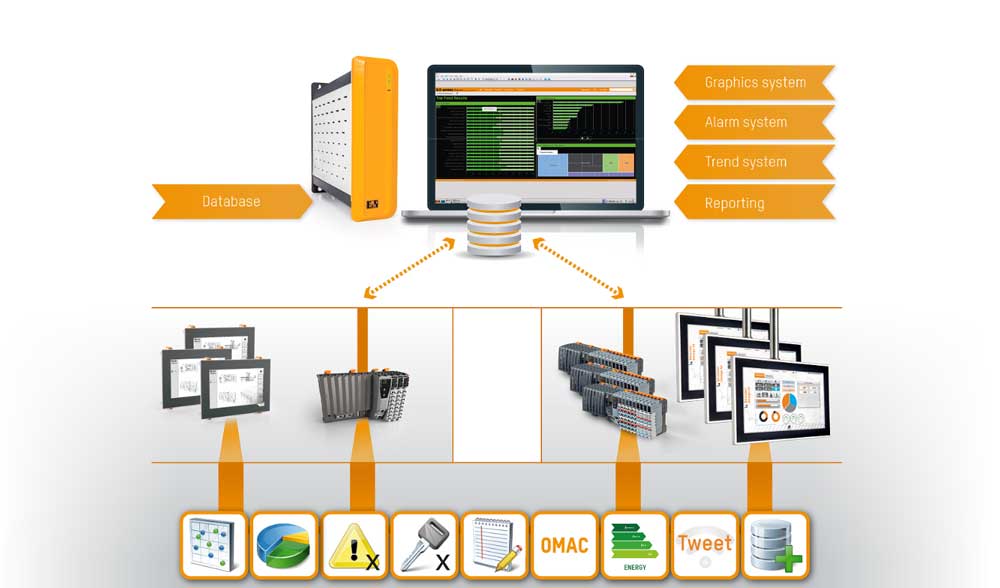
The food industry is one of the industries we cannot do without. Recent uncertainties have just propelled the demand curve, which has seen the market for packaged foods grow multi-fold. Driven by consumer lifestyle changes, the packaging of dry food products has transformed from essentially functional to a highly influential factor in their purchasing decision. Though consumer emphasis on lightweight, flexible, compact, and hygiene-packed food products is increasing, it disrupts the process, such as weighing, handling, sorting, sealing, labeling, wrapping, etc., involved in packaging food products. The shifting preferences boost the demand of the packaging line for more flexibility and efficiency to maximize throughput. The food processing industry is deemed to innovate and advance the packaging process with technology-enabled solutions to meet the growing demands.
Food products are typically manufactured in large volumes, and packaging lines need to synchronize with the process to meet production goals. It involves seamless packaging machinery from primary, secondary packaging to the end of line solutions. Manufacturers are challenged by increasing batch size variability, shorter product lifecycles, unpredictable demand fluctuation, and product proliferation from the single-use pack, films, wraps, bottles to containers used to pack food products in powder, grains, and grains granulate form. Therefore complete visibility of the process chain becomes crucial for manufacturers to address unique requirements from consumers and set new standards in flexible, productive, and efficient packaging. Data-driven models supported by advanced factory automation solutions enable manufacturers to make informed decisions and boost productivity and availability of packaging lines.
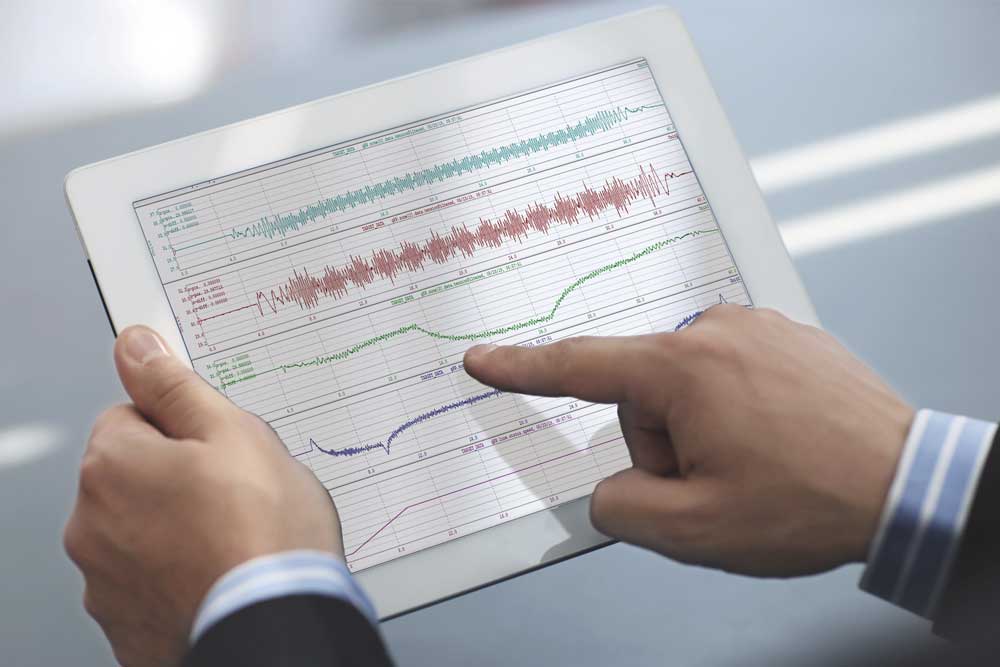
Real-time assessment of packaging line
Edge Controller, the factory automation solution from B&R, enables manufacturers to integrate machines on the packaging line and manage them seamlessly using a single system. Edge controller is a scalable and flexible system consisting of core components for operation and data management, making it a more robust and successful solution among the food processing industries. Edge Controller consists of ready-to-use modules that allow factories to monitor, assess, and optimize production processes. With the integrated PDA (Process Data Acquisition) function, the manufacturer collects, processes critical parameters, and performs analytics.
Data being a key enabler for monitoring production, it is handled with ease using the PDA function. Data aggregated from the packaging line are processed and shared in real-time to factory managers to support making an informed decision. The PDA function’s scalability enables the implementation application to handle several hundred thousand data points in a single system. PDA is integrated with a robust business intelligence suite. With its user-friendly report design tool, manufactures can create customized reports that support all types of data sources. PDA offers intuitive dashboards and graphs that reflect production performance in real-time. It is enabled with powerful and long-time archiving that supports manufacturers to perform a detailed analysis of line performance.
Manufacturers adopt different packaging techniques based on the product lineup, such as zipper packs, aseptic packs, wraps, etc., and each process uses a unique set of data points operations. The Edge controller is easily configured to handle multiple products on the same packaging line. With advance and modular software blocks, this PC-based system can be programmed to handle production with ease. In addition, manufacturers benefit from recipe management, user management, alarms, and trends that are essential software blocks to manage individual products effectively.
End to end shop floor integration in a secured way
Edge Controller brings in the transparency of shop floor data by integrating multi-vendor machines on the packaging line. It supports open communication protocols such as OPC UA and MQTT that enable the production line to connect and share data mutually with IT systems in a unified and more accessible way, thereby offering complete visibility of end-to-end operations on the shop floor. With the increased volume of data, there is also raised concern on data security by the manufacturers. They are keen on ensuring data generated from the process line is accessed only by authorized personnel.
Hence it adds to the responsibility of the automation system to address data security demand. Edge Controller uses best-in-class security features to ensure data is secure throughout the operation. Its integrated security cell provides simple yet efficient protection for systems against malicious software and cyberattacks. Edge Controller functioning over LINUX operating systems gives an added benefit to performing reliable and secured handling of process data.
Increased uptime for increased profitability
Manufacturers have the essential task of ensuring machine availability for continuous operation to achieve production goals. Growing demand from the market forces manufacturers to run machines and packaging lines for long hours affecting the critical and complex motion components. The breakdown of such features brings the complete line to a standstill, affecting the production cycle and incurring loss to manufacturers. Exposure to chemicals, extreme temperature, vibrations, wear and tear, wash-down environments contribute to premature failures of the packaging line.
Packaging lines handling food products suffer from spillage of raw material, waste deposition on equipment that generates a short circuit on electrical systems. Downtime of the process line also disrupts the quality of the product, especially food grade types. In addition, the usage of aging machines on the packaging line needs continuous monitoring and periodic maintenance to increase uptime. It has added pressure on maintenance personnel to adopt an effective maintenance practice to reduce breakdown and increase line availability economically.
Edge Controller proves to be a single system for performing predictive maintenance using its integrated ConMon (Condition monitoring) solution. With ConMon, manufacturers can determine the early warning signs of a breakdown in the packaging line. ConMon solution is built with intelligent algorithms to monitor vibrations anticipate failure at critical points, and minimize line downtime. It makes the diagnostic process more accessible and reduces the time devoted by the maintenance team for routine inspections. It offers a real-time view of operation to the maintenance team and alerts them when the vibration and heat increase above a particular range. In addition, ConMon solution provides maintenance data in the report and graphical format, aiding maintenance experts to perform root cause analysis. It provides an effective monitoring solution for manufacturers that ensures the packaging line’s reliability and makes maintenance most efficient.
More innovative future with B&R
The food processing industry is on the verge of rapid growth. Increasing market demands drive manufacturers to take the extra mile to stay ahead of the competition and become profitable. As packaging trends and consumer preferences are dynamically changing, adopting a scalable factory automation system is critical to creating a differentiation factor in the market. Edge Controller from B&R helps manufacturers design a highly flexible and efficient packaging line with a single system incorporating scalable control, process data acquisition, and condition monitoring. With powerful software and scalable hardware, Edge Controller brings flexibility to the production line and makes them future-ready.